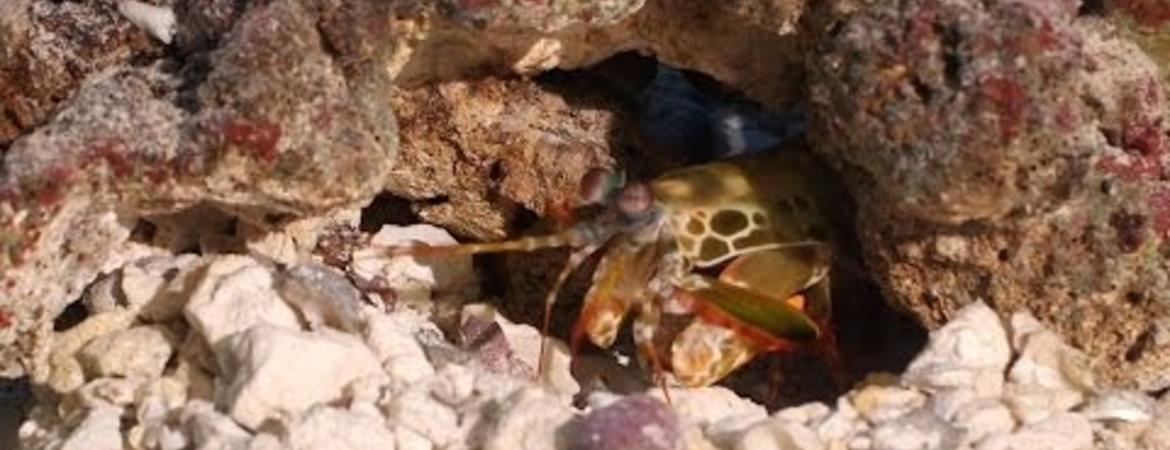
What’s faster than a speeding bullet and more powerful than a locomotive?
Superman, of course. But if you said the dactyl club of the mantis shrimp, you’re half right.
This pugnacious crustacean whips its arm-like club faster than a .22-caliber bullet with a force strong enough to shatter crab or clam shells — though not quite as strong as a train.
How does it do this without breaking its own club?
In a new paper published this month in the International Journal of Solids and Structures, a team of researchers at Purdue University, in collaboration with University of California, Riverside, reveal that upon impact, tiny cracks twist down a spiral structure within the club and not only prevent the shell from breaking, but make it stronger.
David Kisailus, the Winston Chung Endowed Professor in Energy Innovation at UC Riverside’s Marlan and Rosemary Bourns College of Engineering, and Pablo Zavattieri, a professor at Purdue’s Lyles School of Civil Engineering, have worked for more than seven years to unravel the secret of the mantis shrimp’s shatterproof club.
Like the shells of all crustaceans, the mantis shrimp’s club is made of chitin, a tough glucose derivative found in insect exoskeletons and fish scales. In previous work, the team identified three distinct regions with different properties that together contribute to the dactyl club’s unique strength and toughness.
The club exterior has a hard coating that transfers its tremendous momentum on impact to crush prey. The sides of the club consist of a striated region made up of aligned fibers wrapped around the club. Like the hand wraps used by boxers when they fight, the striations compress the club and prevent catastrophic cracking.
The core of the club contains a special structure made of multiple stacks of chitin fiber layers arranged in a spiral-like or helicoidal staircase. Prior research, published in Science and Acta Biomaterialia, revealed the presence of the helicoidal structure within the club and confirmed its significant toughness over aircraft composites.
The initial work showed that the spiral structure minimizes the destructive effect of cracks by twisting them along the spiral, preventing them from radiating in a straight line from the point of impact and breaking the shell. But a detailed analysis of the mechanics of twisting cracks in a composite spiral structure of this type had never been done before.
“This exciting new analytical, computational and experimental work, which follows up on our initial biocomposite characterization of the helicoid within mantis shrimp’s club and biomimetic composite work really provides a deeper insight to the mechanisms of toughening within this unique structure,” Kisailus said.
The team made glass fiber and epoxy composites and 3D printed models based on scanned specimens, and hit them with a force equivalent to what a dactyl club would experience when hunting prey. Researchers filmed the results and also used computer modeling for better visualization.
They found that each time the spiral made the crack change its trajectory, the amount of force needed for that crack to travel further increased until there was not enough energy left to keep the crack going. By keeping cracks near the spiral’s core while simultaneously allowing other cracks to initiate and grow, twist cracking paradoxically improved the club’s resistance to cracking.
When the researchers repeated the test on small segments taken from mantis shrimp clubs, the results meshed nicely with the outcomes of the experiments on 3D models and computer simulations. The results also support the hypothesis that crack twisting helps increase fracture resistance in similar spiral-shaped composite structures.
“This mechanism has never been studied in detail before,” Zavattieri said. “As a crack twists, the driving force to grow the crack progressively decreases, promoting the formation of other similar mechanisms, which prevent the material from falling apart catastrophically. I think we can finally explain why the material is so tough.”
The findings are now helping the development of lighter, stronger, and tougher materials for many applications including aerospace, automotive, and sports.
In addition to Kisailus and Zavattieri, authors include Nobphadon Suksangpany, a Purdue doctoral student; Nicholas A. Yaraghi, a UC Riverside doctoral student; and R. Byron Pipes, a distinguished professor of engineering at Purdue.
The research is funded by the National Science Foundation, U.S. Air Force Office of Scientific Research, Multidisciplinary University Research Initiative, and the National Science Foundation through a CAREER award to Zavattieri.